Making the Body
Laminating Wood Veneers to Form the Rim
Let's focus on the making of the rim first.
The photographs below show wood veneers that are glued together lengthwise to form a layer of the piano's rim. These layers are joined together to make a single long board by being glued and laminated. The number of laminations of these layers varies depending on the model, but is usually from 6 to 10.
Once the long laminated wood board is complete, it is placed in a press that uses high-frequency energy to heat the wood, and hydraulic pressure to press the board into a large mold that has the distinctive shape of the piano case. Resin-impregnated paper is then glued to the outside of the rim to provide a receptive surface for later finishing process.
The inner rim that forms a frame on the inside of the rim is made in a similar fashion.
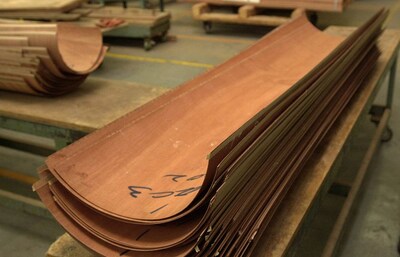
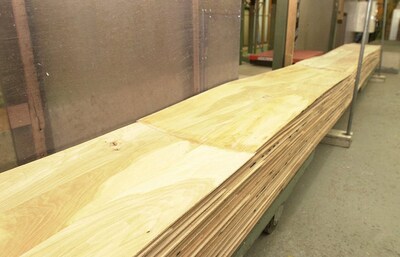
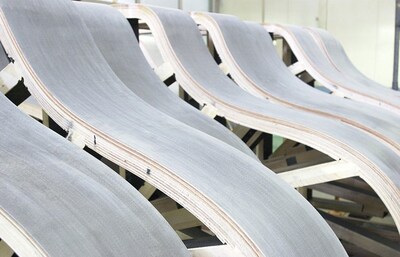
Combining the Inner and Outer Rim
Next, the inner rim that supports the curved contour of the outer rim is assembled with straight beams to form the structural framework of the piano. The beams are notched into the inner rim using traditional dovetail joints, and the surface is planed flat.
The soundboard will later rest on the inner rim, which is milled to accommodate it. The top of the soundboard has a crown (a slight dome) that arches upward toward the strings, and the top surface of the inner rim is cut to match its slope angle. In addition, a number of reinforcing ribs are glued to the underside of the soundboard, and slots are milled into the inner rim where these ribs will fit. Finally, the outer rim, which has been seasoned at a specific temperature and humidity, is joined with the inner rim into a single unit using high-frequency induction heating.
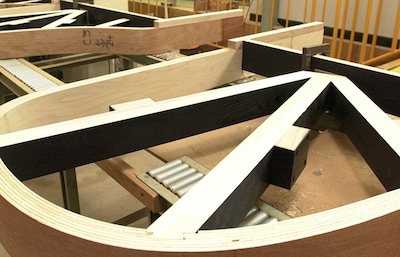
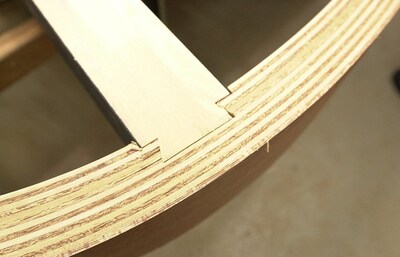
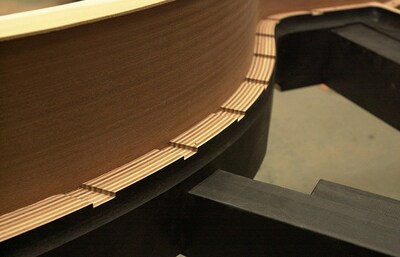
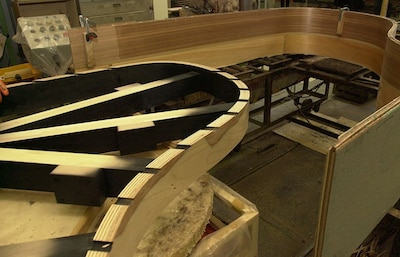
Finishing
A robotic system is used for the finishing process. First, an undercoat is sprayed on and kept warm so that it dries and hardens quickly. The final topcoat is applied in the form of an extremely fine mist, followed by a polishing process that results in an attractive, beautifully finished surface.
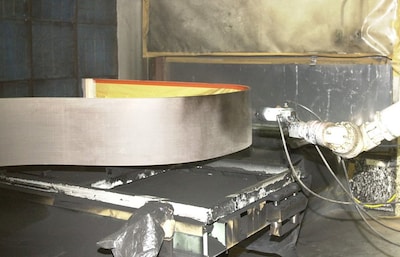
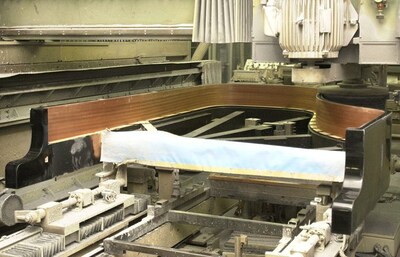
Making the Soundboard, the Part That Determines Tone
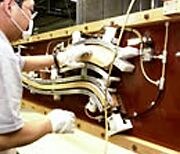
The soundboard is the heart of the piano, and how it is made is an important process in terms of sound.
The soundboard is a thin wooden sheet made from carefully selected Sitka spruce or Japanese spruce. Before being used, the wood is air-dried or kiln-dried to a specific moisture content. The soundboard is assembled from many small planks that are glued together edge-to-edge. The large sheet is cut into the desired shape and planed down to the proper thickness. It is then seasoned (dried) specifically to match the climate conditions where the buyer of the piano lives.
Ribs are then glued to the underside of the soundboard, in a direction perpendicular to the grain of the individual boards in the soundboard. This is done so that the sound vibrations are transmitted uniformly throughout the whole soundboard, and serves to reinforce and stiffen the soundboard, which is weak horizontally. The long bridge and the short bridge are attached to the side opposite of the ribs.
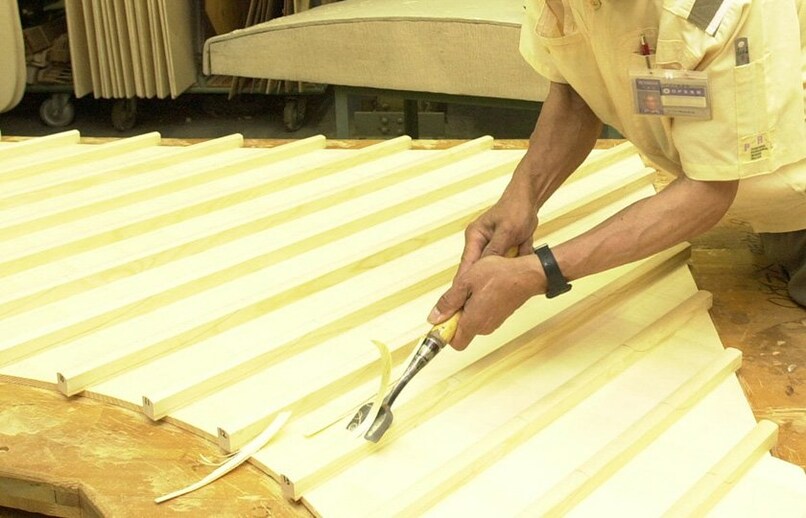
Attach the Frame and the Body Is Almost Complete!
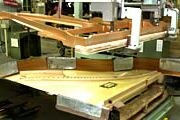
Once the finished soundboard is set in place on the inner rim and the metal frame attached, the piano is almost complete.
The frame is basically cast iron mixed with some additional metals for acoustic properties. The metals are melted, mixed, and poured into a mold made of sand to cool and harden. The frame weighs anywhere around 100 to 150 kg.
Musical Instrument Guide : Piano Contents
Origins
Structure
How to Play
How the Instrument is Made
Choosing an Instrument
Care and Maintenance
Trivia
- The White Keys and Black Keys Were Reversed on Pianos in Mozart's Day
- Did Mozart's Piano Have a Pedal-Board?
- Piano with Automatic Accompaniment System in Beethoven's Day
- The Pianos Beloved by the Great Master, Sviatoslav Richter
- The Optimal Material for Piano Frames Is Also Ideal for Motorcycle Engines
- The Piano Soundboard Is a Board that Also Stops Vibrations
- Why Can't There Be More Than 88 Keys on a Piano?
- Why a Grand Piano Keyboard Feels Heavier Than an Upright Keyboard?